PDT Laser Brazing Head
Description
PDT Laser Brazing Head
Specifications |
|
---|---|
Aperture: | -- mm |
Focal Length: | 200 mm |
Max Laser Power: | 6000 W |
Laser Type: | Fiber, DPSS (Nd:YAG), Diode |
Laser Machine: | Cutter, Welder |
Features: | Other (see Data Sheet) |
Weight: | 11 kg |
Features
- Optimized modular optical systems
- Optic modules with focus forming
- Tactile seam tracking with servo motor support
- Accurate adjustment of wire/tactile sensor
- Wide angular sensor range for optimized component access
- Absolute values for process point
- Direct control via Interbus (or similar)
- PC program for parameter set-up
- System integration
- Cross jet for extended cover slide life time
- CCTV viewing system with integrated illumination of process point
- Robot adaptation with crash sensor
- Interface to PLC
Applications
For pricing, technical or any other questions please contact the supplier
- No registration required
- No markups, no fees
- Direct contact with supplier
-
Ships from:
United States
-
Sold by:
-
On FindLight:
External Vendor
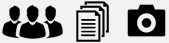
Claim II-VI HIGHYAG Page to edit and add data
Frequently Asked Questions
The processing head can traverse the laser focus to the precise welding or brazing position and then safely and accurately guide it over the workpiece during the process. This compensates for tolerances of the component part and inaccuracies of either the programming or the handling machine. The path can remain unchanged, thus significantly simplifying control.
Yes, there is a PC-based user interface for parameterization of the head (control functions, inputs and outputs).
The PDT Laser Brazing Head offers optimized modular optical systems, optic modules with focus forming, tactile seam tracking with servo motor support, accurate adjustment of wire/tactile sensor, wide angular sensor range for optimized component access, absolute values for process point, direct control via Interbus (or similar), PC program for parameter set-up, system integration, cross jet for extended cover slide life time, CCTV viewing system with integrated illumination of process point, robot adaptation with crash sensor, and interface to PLC.
The PDT Laser Brazing Head is used for laser welding or laser brazing of fillet and edge-formed seams, such as welding trunk lids, roof and sealing duct brazing, or brazing and welding overlap joints.
The tactile servo motor assisted seam tracking is a feature of the PDT Laser Brazing Head that involves a tactile sensor finger, optionally with or without a wire, via an optic-mechanical rotary motion that is directly coupled with the focus guidance system. This allows for accurate adjustment of wire/tactile sensor and wide angular sensor range for optimized component access.